Accelerated Construction Techniques (ABC and PCPS)
slide 1: Accelerated Construction Techniques
Jagannath Mallela
Applied Research Associates, Inc.
June 5-6, 2012
Denver, CO
slide notes:
None
slide 2: Accelerated Bridge Construction
- Objectives
- The reasons for using ABC/PBES
- Definitions of ABC/PBES
- Benefits of ABC/PBES
- Focus Areas
- The status of EDC deployment goals for ABC/PBES
slide notes:
In this module we will go over:
- The reasons for using ABC/PBES
- Definitions of ABC/PBES
- Case studies of ABC/PBES
- Benefits of ABC/PBES
- The status of EDC deployment goals for ABC/PBES
slide 3: Reasons for Using ABC
slide notes:
None
slide 4: Present & Future Challenges
|
![]() |
slide notes:
As you already know, we are challenged by:
- Aging Infrastructure . . . 1/3 of the Nation's Bridge Inventory is in Poor Condition
- Our transportation network experiences increased Traffic volumes every year Between 1998 & 2020 we can expect to see a 70% Increase in Freight Tonnage and by the year 2020, 90% of Urban Interstates are Expected to exceed/approach their capacity
- Highway Construction costs for bridges are extensive – Cost to Maintain our Bridges is expected to amount to over – $176.0 Billion over the next 20 years (2005 to 2024) – or $8.8B annually.
slide 5: Work Zone & Congestion Impacts
Work zone:
|
Congestion:
|
slide notes:
Work zone Impact:
- In the transportation infrastructure renewal program, impacts from increasing work zones is almost certain.
- A study in 2003 reported the total number of highway work zones in the summer was estimated to be more than 6,400 – which corresponded to over 6,000 lane miles closed.
- That amounts to 20% of the capacity reduction on our national highway network!
Congestion Impact:
- One business at a time, and one commuter at a time - congestion robs our nation of productivity and quality of life.
- Based on TTI 2007 Urban Mobility Report (437 urban communities) congestion translates to:
- 4 billion hours/year in time delays
- 2.9 billion gallons of wasted gas/year
- $78.2 Billion cost to travelers (Based on gas price in 2005.)
- Total congestion cost for the 437 urban areas came to almost $78.2 billion per year.
slide 6: More Challenges Ahead
- Globalization of manufacturing increases demands on our transportation Intermodal networks
- 1 M more truck traffic by 2016 (ATA)
- More drivers on highways
- Urban Sprawl Continues
slide notes:
The American Truckers Association reports that by 2016 our highways will carry 1 million more trucks. This is caused by trucker's hours-of-service regulations – which prevents haulers from operating their rigs for more than 11 hours/day and for more than 70 hours per eight-day period.
As quoted by B.J. Gorman, president of Tango Transport Inc. of Shreveport, LA. (ref. AASHTO Journal, September 15, 2006), "One reason for trucks' popularity is that they become de facto warehouses as the result of our modern inventory-control systems. This is a service other forms of transport can't supply."
and ATA's Chief economist Bob Castello reported that there are 2.7 million big rigs on U.S. Highways as of 2006.
slide 7: Definitions of ABC/PBES
slide notes:
What are Prefabricated Bridge Elements & Systems and how do they Accelerate Bridge Construction projects?
slide 8: Accelerate Bridge Construction (ABC)
ABC (v): The use of innovative planning, design, materials, and construction methods to reduce onsite construction and mobility impact times
PBES are structural components of a bridge that are built offsite, or adjacent to the alignment, and includes features that reduce the onsite construction time and mobility impact time that occurs from conventional construction methods.
slide notes:
We define Accelerated Bridge Construction as bridge construction which use innovative planning, design, materials, and construction methods in a manner to specifically reduce the onsite construction time and mobility impacts that occur when building new bridges or replacing and rehabilitating existing bridges.
Use of prefabricated bridge elements and systems (PBES) is one strategy that can meet the objectives of accelerated bridge construction.
PBES are structural components of a bridge that are built offsite, or adjacent to the alignment – and includes features that reduce the onsite construction time and mobility impact time that occurs if conventional construction methods were used.
By building the structural elements, or the entire bridge offline, the onsite construction period can be condensed and the mobility impacts to the transportation network can be reduced – like in hours or in a weekend!
However, there are other common and equally viable reasons to use PBES which deal with site constructability issues. Oftentimes remote site locations, limited construction seasons, material availability, and consistent quality in workmanship present opportunities where the use of PBES can provide more practical and economical solutions over conventional construction methods.
Regardless of the reason(s) to choose PBES, On-site construction time and Mobility impact time are typically reduced in some manner relative to conventional construction methods.
slide 9: Benefits of ABC/PBES
slide notes:
None
slide 10: Benefits of ABC with PBES
ABC / PBES improves:
ABC / PBES reduces:
ABC / PBES can minimize:
|
![]() |
slide notes:
ABC offers benefits to the traveling public
However, ABC by itself can simply be a matter of providing more onsite labor, equipment, and contracting mechanisms (like I/D clauses) to meet the need to "get in/get out/stay out."
But when we use PBES to accelerate bridge construction – we not only meet the objectives of ABC, we do so in a more efficient manner and realize additional benefits as well. By replacing conventional on-site construction activities with prefabricated elements and systems, the benefits of ABC expand and compound.
For example, the safety of the traveling public in addition to the safety of the contractor's personnel improves. Improvements in product quality and long term durability can be better achieved, the opportunity for weather related time delays become less, and the on-site project disruptions which can directly influence the existing roadway alignment, environmental impacts, ROW, and Utility disruptions can be minimized even further.
More notes...
Reduces On-Site Construction Time:Using prefabricated bridge elements and systems means that time consuming onsite construction activities such as formwork construction, re-bar and concrete placement, concrete curing, formwork removal and other related tasks including the planning, coordination, and scheduling efforts for the on-site labor, material, and equipment can be done off-site and off the critical path.
Minimizes Traffic Impacts: Prefabricated bridges minimize traffic impacts by reducing the amount of on-site construction time. This reduces lane closures, detours, and traffic delays which results in improved safety for the traveling public.
Improves Work Zone Safety: Because on-site construction times are reduced when PBES are used, work zone safety can be greatly improved upon. Construction workers spend less time near high traffic volumes, power lines, and over elevated work areas. The durations of exposure to extreme weather conditions which influence worker fatigue also becomes less.
Improves Site Constructability: When we discuss the need to improve On-site Constructability, we speak of the project sites that impose constraints to the constructability of bridges. Examples include heavy traffic on an interstate highways, difficult elevations, long stretches over water, restricted work areas due to adjacent facilities such as utilities and buildings, and detour routes that aren't feasible nor practical.
Areas that experience high traffic volumes, either with or without congestion in terms of ROW and utility impacts are common in urban and major metropolitan areas.
However, rural areas also experience their share of difficult site conditions.
Increases quality: Prefabricating the structural components of a bridge takes them off the critical path of the project schedule: work can be done ahead of time, using as much time as necessary, and it can be done so in controlled environmental conditions.
This reduces the dependence on weather, and can improve the control of quality of the resulting elements and systems.
slide 11: FHWA Every Day Counts ABC Focus Areas
slide notes:
None
slide 12: Focus Areas
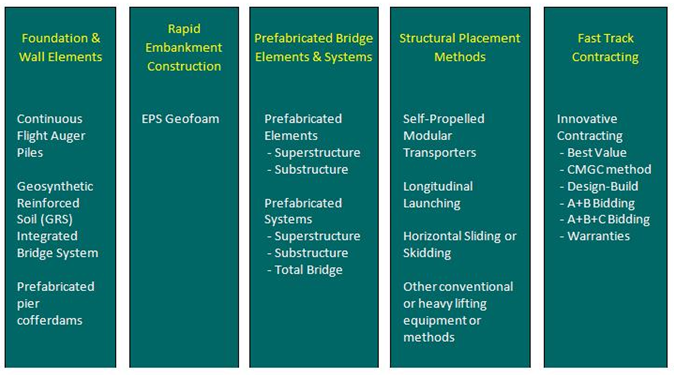
slide notes:
None
slide 13
![]() Prefabricated Cantilever Abutment (Source: FHWA ABC Manual) |
![]() Partial Depth Precast Deck (Source: FHWA Highways for Life) |
![]() Sliding (FHWA HfL) |
![]() Precast Open Frame Pier Bent (Source: FHWA ABC Manual) |
![]() Bridge Move with SPMT (Source: FHWA Highways for Life) |
![]() Bridge Move with SPMT (Mammoet) |
![]() Strand Jack Lifting (Mammoet) |
![]() |
![]() |
slide notes:
None
slide 14: ABC Decision Framework
slide notes:
None
slide 15: Decision-Making Flowchart At-a-Glance
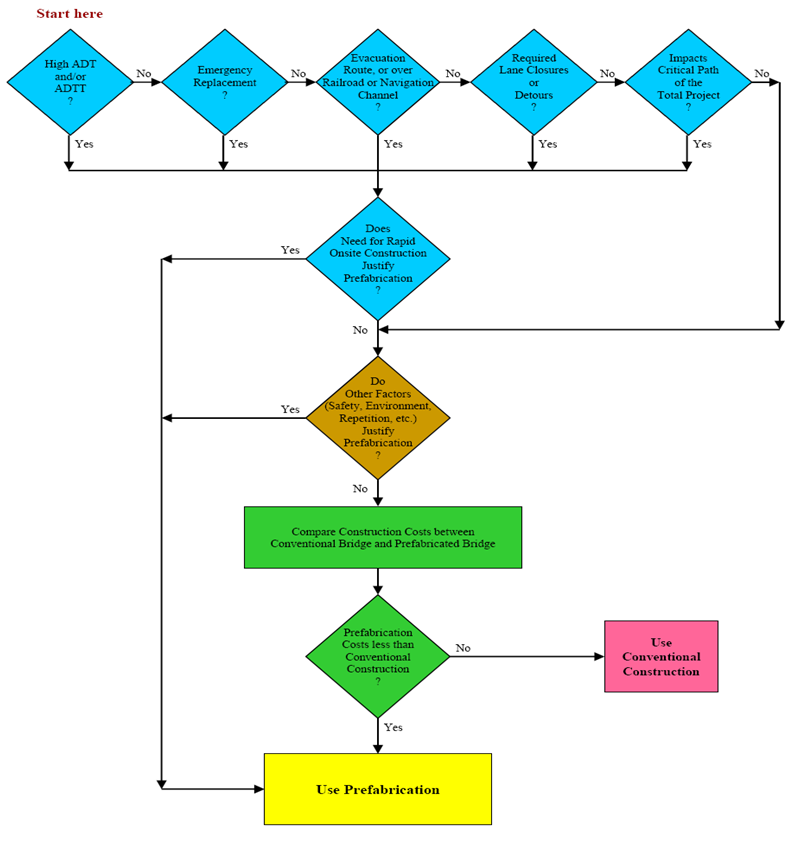
slide notes:
The one-page flowchart allows decision-making at a glance, for example, for a high-level decision-maker who wants a high-level tool for a quick decision without getting into the technical details of a project.
Note the color-coded categories. The blue diamonds are related to rapid construction issues (factors). The tan diamond is related to other issues that may drive a project. The green rectangle and diamond are related to cost issues. These three categories are consistent throughout the framework.
slide 16: The Status of EDC Deployment Goals for ABC/PBES
slide notes:
None
slide 17: Pursuing PBES for EDC

slide notes:
This is a map showing how many Agencies that reported a commitment to using PBES as part of their EDC deployment goals.
44 out of 55 Agencies
Note: Data validation may be further required.
slide 18: Current Status
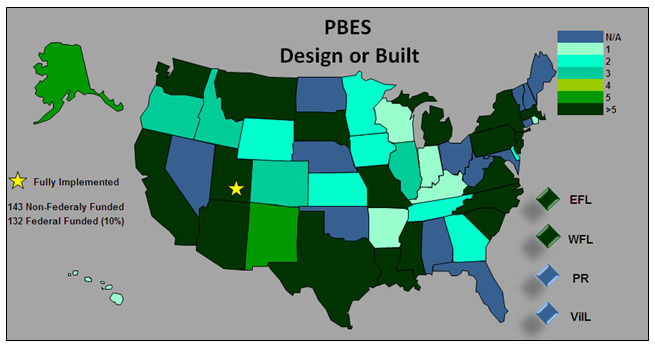
slide notes:
None
slide 19: Conclusions
Advantages:
- Faster (offsite & off critical path)
- Safer (public and construction)
- Better Quality (controlled environment)
- Lower Cost (total project/life cycle costs)
- Easily adaptable to many site constraints
slide notes:
Why are we championing the use of PBES technologies? It offers significant advantages.
- Faster (offsite & off critical path)
- Safer (public and construction)
- Better Quality (controlled environment)
- Lower Cost (total project/life cycle costs)
- Easily adaptable to many site constraints
slide 20: Questions?
FHWA Contacts:
PBES Innovation Team
Benjamin Beerman, Team Lead
benjamin.beerman@dot.gov
slide notes:
None
slide 21: Precast Concrete Pavement Systems for Rapid Repair, Rehabilitation, and Construction
slide notes:
None
slide 22: Accelerated Construction of Concrete Pavements
Precast Concrete Pavement Systems (PCPS) for concrete pavement construction
- Momentum is growing
- Demonstration projects and pilot projects
- Innovations and modifications
- Specifications
slide notes:
None
slide 23: PCPS Attributes
- Improved quality and performance
- Accelerate construction
- Reduce work zone size and times
- Reduce safety risks
- Reduce risk to contractor and owner agency (use specific terms)
- Extended construction season
- Reduced costs
slide notes:
PCPS have many proven attributes that make a real difference:
- Improved quality through controlled conditions like high performance concrete and self consolidating concrete
- Shorter total construction times
- Tighter work windows at off-peak times and tighter work zones.
- Reduced worker and motorist exposure to work zone conflicts.
- Reduced construction risks because variable field conditions are taken out of the equation.
- Can work later in season by curing concrete in controlled environment
- Reduced life cycle costs and eventually first costs with standardization and familiarity
slide 24: PCPS Basics
- Fabricated off-site
- Transported to the project site
- Installed on a prepared foundation
- No field curing or time to achieve strength
- Two main categories
- Jointed Systems – Include system specific joint design
- Example – Super-Slab and several other generic systems
- Prestressed Systems – Use a combination of pretensioning (plant during fabrication) and post-tensioning (installation)
- Example – Precast Prestressed Pavement System (PPCP)
- Jointed Systems – Include system specific joint design
slide notes:
As most of you are aware, the use of precast building elements has a series of benefits when compared to traditional Cast-in-place methods. The Precast factory environments help to control tight dimensional tolerances, higher quality control than field controls, and provides a controlled curing environment all resulting in less residual stresses in the slabs and improved long-term performance of the products. Prestressed systems offer the ability to provide thinner pavement sections without sacrificing increase fatigue on the pavement . Placement of these precast slabs is not dependant on the weather; thereby, potentially extending the construction season. The Precast Pavement Slabs are installed on prepared foundations and when combined with bedding fill materials the slabs become fully supported.
Applications of PCPS are often referred to as either intermittent or continuous. Intermittent is when within a given highway segment localized severely distressed PCC slabs adjacent to healthy pavements are removed and replaced with Precast Concrete Pavement System slabs, thereby, raising the remaining service life of this highway segment. The other application is continuous placement applications, such as in project level rehabilitation or reconstruction.
slide 25: Recent Project Example – I-66 WB, Fairfax, VA
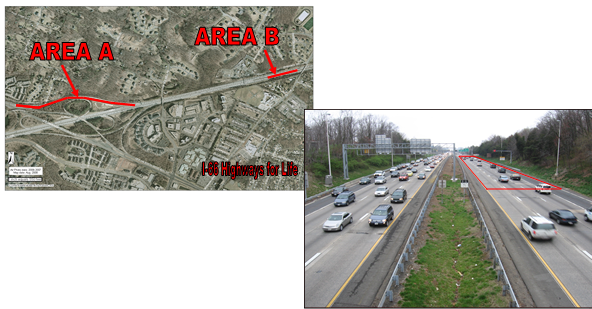
slide notes:
None
slide 26: Jointed PCPS - Super-Slab® Pictures (From I-66 VA and Tappan Zee Toll plaza)
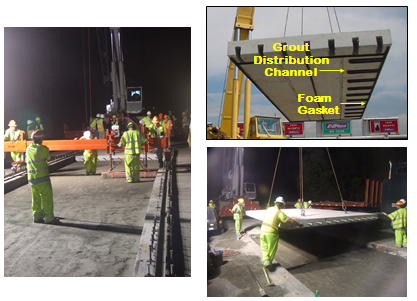
slide notes:
None
slide 27: PPCP Pictures (From I-66 VA)
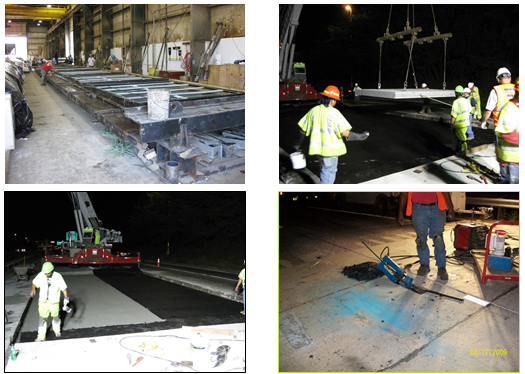
slide notes:
None
slide 28: Applications
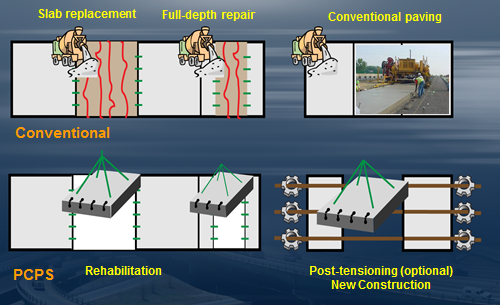
slide notes:
What this schematic diagram illustrates is the differences between conventional cast-in-place rehabilitation and new construction techniques and the use of Precast Concrete Pavement Systems. In the rehabilitation applications comparison, you see the use of jointed PCPS slabs being employed in lieu of traditional CIP methods. For new construction, the use of either jointed or prestressed/post-tensioned applications can be employed as an alternative to traditional CIP paving methods.
Applications:
- Mainline rehabilitation and new construction
- Ramps & interchanges
- Bridge underpass (increase vertical clearance)
- Intersections
- Bridge approach slabs
- Sensor (RFID readers) embedment in the PCPS Panels
slide 29: PCPS General Terminology
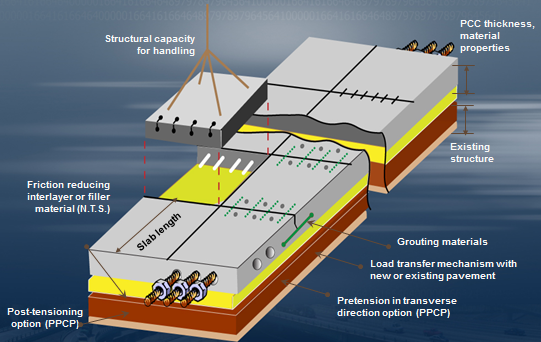
slide notes:
To ensure that all of you have a clear understanding of what Precast Concrete Pavement Systems are, the pavement cross-sections and schematics above are meant to generically illustrate some of the key features of any PCPS system. When we talk about these Precast Concrete Pavement Systems, they truly are a paving system. There are two types of PCPS systems: one is a Jointed PCPS system, and the other is a Prestressed PCPS system. Key to each system is the need to clearly identify such items as: sub-base preparation, slab bedding material, slab geometry limitations (2-D, 3-D, factory & field tolerances), fill material for any under slab voids to ensure a uniformly supported slab, load transfer methodology and associated fill material to lock these in, pre and post-tensioning tendons sizing, tensioning and grouting requirements, lifting arrangements and hardware, are all considered integral elements of these Precast Concrete Pavement Systems. Although we speak here in generic terms, each PCPS system employs a different approach to these common elements.slide 30: States with PCPS Experience
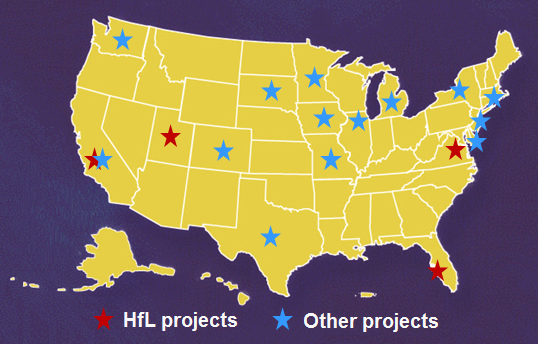
slide notes:
Several States have undertaken projects and have considerable experience with PCPS as indicated.
slide 31: Project Level Decision Logic
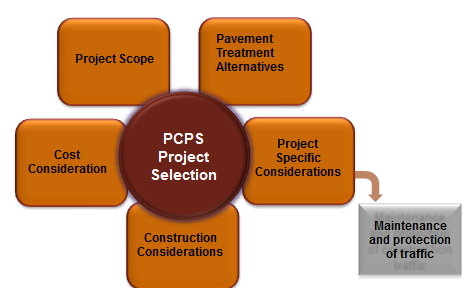
slide notes:
For the next few minutes I'd like to walk you through what I consider the necessary inputs and factors that influence the Project Level Decision logic to evaluate the technical and economic feasibility of selecting PCPS treatments for PCC pavements over other traditional treatments.
slide 32: Project Level Decision Logic
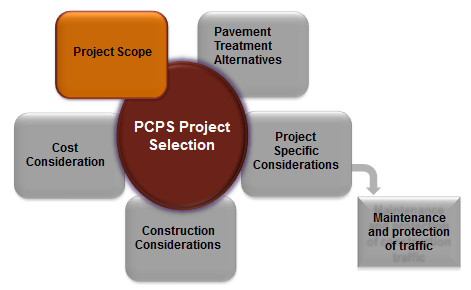
slide notes:
We'll begin the process by looking at Project Scoping
slide 33: Project Scope
- Pavement service life and objectives
- Current & projected traffic density
- Slab replacement criteria
- Estimated project duration
- Work window options
slide notes:
The decision tree logic that I refer to is a series of go-no-go or if this existing condition exists, then our choices are the following...This decision process is one that most Pavement Engineers are familiar with. Project level scoping follows the traditional approach, looking at the project objectives. Is this a short-term project where we're more or less patching the pavement to buy us 5 to 10 years before a scheduled reconstruction project comes in, or is this more of a permanent treatment that is expected to last 40 to 50 years or more.
Pavement distress identification follows traditional windshield level or crack survey methods. Some states have more detailed Slab Replacement Guidelines to provide additional guidance to engineers. [CALTRANS has an excellent Slab Replacement Guideline that is on-line] Included in the pavement evaluation should be investigation that includes sub-base, drainage, evaluation of Load transfer efficiency across existing joints, etc. Many of these rehabilitation projects may employ a combination of CPR and slab replacement techniques.
Lastly, to help us evaluate various pavement treatment options, we need to know the expected project duration and the available work window options. Based upon existing and projected traffic density, what are the lane occupancy limitations or restrictions surrounding this project? As we will see later, this is probably one of the most critical decision inputs.
Keep in mind that during the construction sequencing of installing PCPS, it is generally accepted that a working width of at least two lanes (24 ft.[7.3m]) or one lane plus an adjacent shoulder (total width of 22 ft [7.0m]) is required for precast slab installation operations and equipment.
slide 34: Project Level Decision Logic
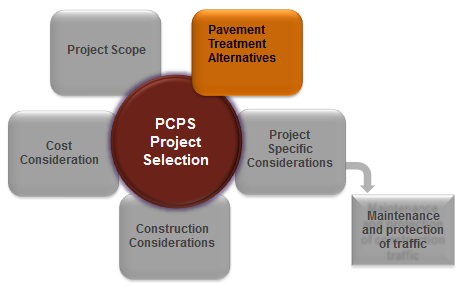
slide notes:
Next we'll evaluate various Pavement Treatment Alternatives
slide 35: Pavement Treatment Alternatives
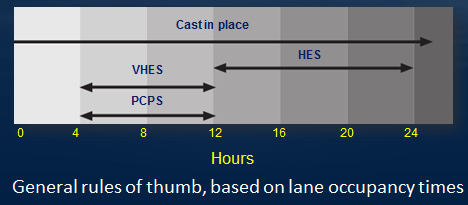
slide notes:
This slide represents some general rules of thumb logic that provide general guidelines in the selection of PCPS systems. The availability of lane occupancy (or lane closure) will help you determine the type of PCC Pavement Treatment.
When there is greater than 24 hours cure time available, such as in total long-term lane closures and/or temporary traffic crossovers or detours, then traditional Cast in Place treatments will be the most cost effective. Thereby, providing sufficient curing time to produce durable pavements of adequate strength. Typically 10 to 14 day cure time is required before traffic can be restored.
If the lane occupancy is less than 24 hours, but greater than 12 hours, then probably High Early Strength Concrete treatments will be the most cost effective. These are concrete mixes that will develop compressive strengths greater than 21 MPa [3000 psi] in 12-24 hours. Don't forget to consider the time requirements for slab removal, construction and curing operations within this time limit.
When the available work window shrinks to 12 to 8 hours or less, Very High Early Strength concrete is an option, but the use of PCPS becomes increasingly favored because the amount of time available for reliably producing properly cured and durable cast-in-place materials becomes highly critical.
Depending on the project configuration and the associated traffic demands, we have seen combinations of these treatments applied.
When we see these limited work windows, we are also witnessing contractual liquidated damages assigned to contractors as penalties for failing to open lanes on time. These accelerated work windows and the associated potential for liquidated damages equate to risk for both the Owner and the Contractor. We believe that the application of PCPS will reduce that risk; whereby, resuming traffic flow isn't tied to accelerated cure times and associated strength gains of the panels.
slide 36: Project Level Decision Logic
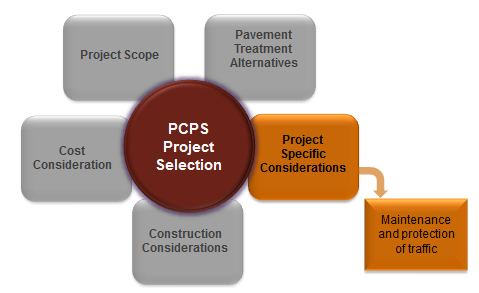
slide notes:
The next input is Project-Specific Considerations
slide 37: Project Specific Considerations
- Need for accelerated construction
- M&PT considerations, seasonal restrictions, stakeholder impact
- Funding guidelines
- Design and engineering data requirements
- Construction risk
- Specifications
slide notes:
To summarize our project scoping phase, we've evaluated the current condition of the PCC pavement and determined that rehabilitation or reconstruction is warranted. We've evaluated traffic flow, density and lane occupancy requirements and have made a determination that Accelerated Construction using PCPS is warranted. Are we still within the project funding limits to support accelerated construction, knowing that PCPS systems will have a slightly higher initial costs?
Ok, now that we've decided on a PCPS treatment, a host of other questions need to be answered. How do we specify a PCPS system? What additional engineering data may be necessary? How do we economically justify PCPS? Are there additional construction risk involved with PCPS applications?
slide 38: Specification Options
- Sole Source Specification
- Preselect PCPS system and work directly with provider
- Multiple Source Specification
- Use PCPS with general performance guidelines
- Generic Specification-Prequalification:
- Use generic performance specifications = Prequalification of Precast Concrete Paving Systems (www.aashtotig.org)
slide notes:
We have seen multiple approaches by owner/agencies to specify PCPS systems. For some of the demo-type projects, owners have used Sole Source Specifications and worked directly with PCPS providers to work out the necessary engineering details. Regarding Federal Aid Eligibility, some of these early projects were accomplished using an Experimental Feature approval with a work plan to evaluate the PCPS method employed. Other states are using Public Interest Findings to work with some of the Proprietary PCPS Systems.
Another option for designers is to develop a generic performance specification; thereby, opening up competition to all PCPS providers. This bring me to what we in the AASHTO TIG Team have been promoting. The use of a generic product approval specification that is used to prequalify PCPS systems and gain acceptance on the DOT's Approved Product List. A draft copy of this specification will be available in mid-June 2008 on the www.AASHTOTIG.org web site.
In addition to the Generic PCPS Approval Specification, the AASHTO Web site also has approximately 10 other proven state specifications for PCPS systems that could be used as a template for your applications.
slide 39: Prequalification of PCPS Gaining State DOT Approval
|
|
Trial installations – prove the PCPS off-site before the project begins |
slide notes:
Included in the Performance Specification for Prequalification Approval is everything an owner needs to know and qualify about particular PCPS systems. Since this is a Pavement System, it is important to know the composite details of the entire system and prove both the construction sequencing and the finished product will perform as required. This approach sets a generic performance standard for all PCPS systems for a given DOT, thereby providing an opportunity for all PCPS systems to become prequalified and approved. Much like other manufactured products that are on a DOT Product Approval Lists, ideally we would like to see multiple PCPS systems become approved, providing a dual benefit of eliminating proprietary product issues as well as creating a competitive environment for these systems. This approach significantly reduces both the contractor and owners risk, knowing that a failure of any one component will severely compromise limited work windows.
As part of this approval process, it requires that PCPS providers demonstrate that they can meet the specification to gain DOT approval.
slide 40: Project Level Decision Logic
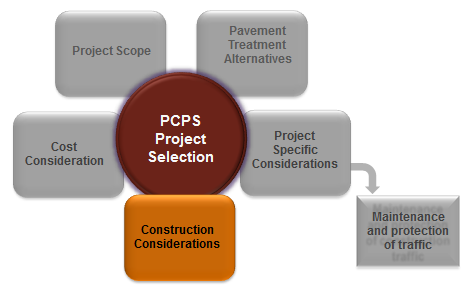
slide notes:
The next level of consideration is construction
slide 41: Construction Considerations
- Qualified precaster presence in area
- Contractor's familiarity with PCPS construction process
- Planning and scheduling
- Quality assurance
- Contract plans
slide notes:
As mentioned, these are some of the implementation challenges that we have seen.
Potentially higher initial costs than traditional or HES mix applications; however, it may quickly become apparent that the use of pavement materials that can be installed quickly and can reliably provide long service life will offset higher initial costs, with substantial savings in future maintenance, congestion, and user cost, especially for heavily traveled urban corridors and intersections: And, history tells us that with any new technique added familiarity, confidence and efficiency gains brings the cost down. What about availability of qualified precast in the area? Will we see increased bid prices due to contractors being unfamiliar with the PCPS construction process? And again, how do we specify PCPS and what additional details or engineering data may be necessary on the contract plans and specifications?
As I've mentioned previously, for the construction sequencing of installing PCPS, it is generally accepted that a working width of at least two lanes (24 ft.[7.3m]) or one lane plus an adjacent shoulder (total width of 22 ft [7.0m]) is required for precast slab installation operations and equipment.
Construction Sequencing somewhat follows traditional slab removal techniques; however, each PCPS system is slightly different in their approach to slab bedding, leveling and load transfer approaches. One of the key attributes of PCPS system installation is that with most systems, you can apply a short-term traffic loading with just sub-base supported slabs; thereby, allowing the contractor to come back during the next lane occupancy opportunity and apply final bedding, load transfer anchorage and embedment and complete the installation.
As you can imagine, there is a learning curve that paving crews will go through to become productive. Usually within a few days to a week or more, the crews quickly come up to optimum production. Many times PCPS system have been compared to Precast Bridge Deck projects, with some truth to that. As a result, you will require a somewhat different skill set for Field Quality Assurance Technicians who may be more familiar with taking slumps, air and making cylinders on more traditional PCC Paving Projects. These new skill sets will require familiarity with testing cementitious or polymer modified grouting materials, High Density Polyurethane foam products, post tensioning stressing of tendons, and a few other non-traditional paving materials testing.
slide 42
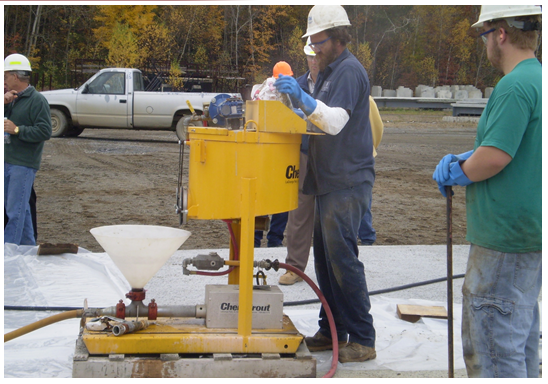
slide notes:
None
slide 43: Project Level Decision Logic
slide notes:
Lastly, we need to consider the cost of these PCPS treatments
slide 44: Cost Considerations
- Should expand beyond initial costs
- LCCA – reduced maintenance costs and user-delay cost
- MTO reports only 10% higher cost than high early strength
- Economies of scale and industry familiarity
- Considerations of Road User Costs appropriate
slide notes:
Economic Justification should go well beyond initial costs of the PCPS system. It should take into consideration savings in user delay costs by using accelerated construction methods leading to less impact to the traveling public, as well as improved worker safety. It should also take into consideration the long term performance of the PCPS systems offer with design lives of 35-50 years.
One of our AASHTO TIG members from the Ministry of Transportation Ontario reported that on one of his recent projects using alternative bidding methods, that PCPS bid prices were only 10% higher than HES alternative treatments.
Lastly, many times engineers rely on historical price data to estimate project costs. With PCPS systems there is very little reliable historic data. Many of what I'll call first generation projects have been demonstration-type projects; however, we are beginning to see the next generation of projects where PCPS systems are being specified as part of mainstream pavement rehabilitation and reconstruction projects. With these projects, improved PCPS cost data will become more readily available. As I mentioned previously, history tells us that with any new technique added familiarity, confidence and efficiency gains brings the cost down.
slide 45: PCPS Summary
- Successful installations nationwide
- Proven long term performance
- Ideal for accelerated construction for projects with lane closure restrictions
- Specification and guidelines available for your use
- PCPS can be added to your PCC treatment toolbox
slide notes:
I hope that over these past few minutes, I've been able to acquaint you with the various Precast Concrete Pavement Systems and their effective applications for PCC Rehabilitation and Reconstruction Treatments. You have heard how PCPS can help to accelerate construction with limited lane occupancy requirements and provide for "Early-Open-to-Traffic" pavement treatments. There are a number of resources available to you to assist you in trying PCPS on a projects. I hope that I have familiarized you with a very generalized approach of properly selecting PCPS and the types of specifications that are available to you. I'm confident that over the next few years, as we get more projects under our belt, that these general guidelines will be further refined.
My personal challenge to you and your agency is to apply these treatments, and prove to yourselves that these are valid PCC pavement treatments that can offer significant advantages to owners and the traveling public. As with all pavement treatment strategies, there is an appropriate time and place where these treatments should be used, to optimize the benefits. We have provided the background and framework for these treatment decisions; The next step is yours!
slide 46: Thank you!!
Jagannath Mallela
ARA, Inc.
(217) 356-4500
jmallela@ara.com
slide notes:
I've included my contact information and I hope that if any of you have questions that extend beyond this videoconference, that you'll call me or drop me a line and I'll get you the answers you're looking for. Now, we will turn over the presentations to Dave Merritt and Peter Smith so they can give you more specific details of a jointed and prestressed/post-tensioned Precast Concrete Pavement System. Return to List of Presentations