Applying Transportation Asset Management to Intelligent Transportation Systems Assets: A Primer
Chapter 6. Maximizing Performance—Lifecycle Planning
Planning for the lifecycle of assets is a foundational principle of asset management. The FHWA encourages transportation agencies to develop and adopt asset management plans that enable them to meet the challenges of preserving their assets while optimizing their performance over asset lifecycles. The maintenance approach for each asset type may differ, depending on its risks and effect on the transportation network. Effective asset management planning is proactive. Rather than waiting for an asset to fail, requiring replacement or costly repairs, preventive maintenance and other proactive interventions may keep costs low and support better system operation (reduce delays).
FHWA TAMP Element: Lifecycle Planning, Risk Management (23 CFR 515.7(b)-(c))
Lifecycle planning is a critical component of asset management, but is most effective when part of a robust asset management program. Lifecycle planning is one of the emerging themes in ITS asset management. Lifecycle planning is a requirement for TAMPs. All major asset classes should have a lifecycle plan addressing future changes in demand, information on current and future environmental conditions, the management/maintenance of the asset, managing risk of asset failure, and other factors that could impact whole of life costs of assets.
Every asset will eventually reach a point of failure, and this timeframe is often referred to as the life expectancy (National Academies 2012). Each asset may deteriorate at a different rate. Figure 5 illustrates various deterioration rates.
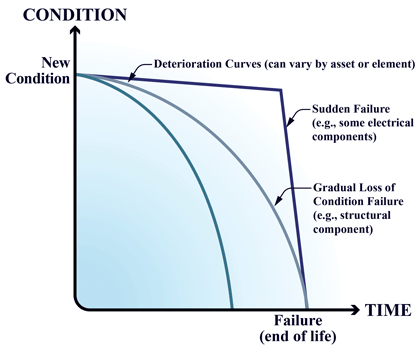
Figure 5. Graph. Asset deterioration curves.
(Source: FHWA.)
A line graph showing various deterioration curves of condition over time. A sudden failure, for example of some electrical component, drops sharply to failure (end of life). Gradual loss of condition failure for example of a structural component, is a more gradual curve and slowly arrives at failure (end of life).
Assets (especially electronic assets) can fail at any time, sometimes unexpectedly. As an asset gets closer to the end of its life, the risk of failure increases. This creates uncertainty in decisionmaking and lifecycle planning that needs to be considered.
Several key concepts that inform asset specific decisionmaking are as follows:
- Maintenance Management—How maintenance decisions are made within an agency. The maintenance management approach will influence the method to estimate the lifecycle cost of managing an asset over its whole life.
- Work Types—The action taken as a result of a life-cycle planning approach. FHWA uses work type categories of initial construction, maintenance, preservation, rehabilitation, and reconstruction.
- Lifecycle Planning—The overall process to estimate the cost of managing an asset, asset class, or asset subgroup over its whole life with consideration for minimizing cost while preserving or improving the condition.
Maintenance Management Approaches
With ITS assets, an agency may consider a range of maintenance management approaches, including the common approaches listed in table 8.
Table 8. Maintenance management approaches for intelligent transportation system assets.
Approach |
Description |
Outcome |
Condition-Based Maintenance Management |
Maintenance activities are scheduled based on regularly monitored performance. Typically, used on assets with long asset lifecycles. |
Approaches can lead to asset preservation approaches. |
Interval-Based Maintenance Management |
Maintenance activities are scheduled at specific time intervals based on an analysis of asset performance. Used on assets with short or long lifecycles. |
Approaches can lead to asset preservation approaches. |
Reactive Maintenance Management |
Maintenance activities are performed in response to reported asset failures or events, such as a vehicle collision or component failure. |
Requires repair/replacement to return service. |
Each approach listed in table 8 can be appropriate for certain assets. The following sections describe each approach and its application.
Condition-Based Maintenance Management
Condition-based maintenance management involves regular monitoring of an asset to assess the point at which repair or replacement is required, as shown in figure 6. The cost to undertake inspections can be high and should be balanced with the associated risk of failure.
Figure 6. Graph. Condition-based maintenance management.
(Source: FHWA.)
A line graph showing condition of an asset over time with condition-based maintenance. As the curve of an asset declines towards the failure (end of life) about halfway down the arc it reaches the marker of treatment timing based on condition trigger point which is a horizontal line at “X percent” coming off the x axis, where it can be either repaired or replaced. At this point it goes up in a straight line to the initial starting point of the first arc on the x axis and then continues a new arc decline.
For ITS assets, the supporting structure for the ITS device, such as a pole or cantilever, should be inspected regularly. Virginia DOT conducts a combination of maintenance management approaches for its ITS assets (or what Virginia DOT refers to as technology assets), including condition-based maintenance of these structures.
Interval-Based Maintenance Management
Interval-based maintenance management is commonly used for ITS assets, and it is a good starting point for planning and predicting needed repair or replacement. Once an asset reaches a specified age it is either repaired or replaced. The age at which an asset must be repaired or replaced varies (sometimes considerably), but this proactive approach reduces the likelihood of asset failure. Interval-based maintenance management relies on information regarding the age of the asset to be able to assess the time to repair/replace. A decision on the best way to predict service life depends on the information available, knowledge of the product, and time available to decide. This information may come from various sources, including the manufacturer, industry best practice, and the agency’s own research. Interval-based preventive maintenance (figure 7) creates an opportunity for operation checks for ITS assets.
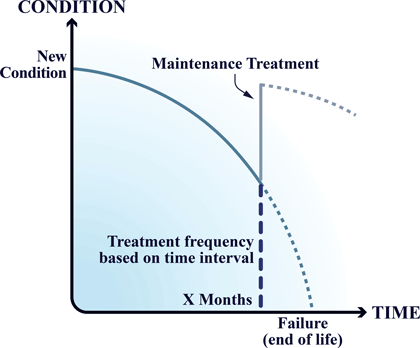
Figure 7. Graph. Interval-based maintenance management.
(Source: FHWA.)
A line graph showing condition of an asset over time with interval-based maintenance. As the curve of an asset declines towards the failure (end of life) about halfway down the arc it reaches the marker of treatment frequency based on time interval which is a vertical line at “X months” coming up off the y axis. At this point the asset receives maintenance treatment and goes up in a straight line to the initial starting point of the first arc on the x axis and then continues a new arc decline.
Condition-Based Lifecycle Management—Virginia DOT
Virginia DOT classifies its ITS assets into two components: the ancillary structure and the technology component (e.g., signal, controller, camera). For the ancillary structure, Virginia DOT assesses the condition of the superstructure (cantilever, parapet mount, and/or span wire) and the substructure (foundation). The condition ratings used for ancillary assets are divided into five categories: good, fair, poor, critical, and failed condition. At the time of each inspection, an inspector assigns condition ratings to describe the major structural components of the asset. Condition ratings are based on criteria similar to those defined by FHWA for bridge inspection. ITS assets are inspected for condition every four years. Figure 8 shows the condition of Virginia DOT’s ancillary structures for three of the five rating categories.
Figure 8. Graph. Virginia Department of Transportation condition of ancillary structures.
(Source: Virginia Department of Transportation, 2018.)
A stacked bar chart showing conditions ratings of Virginia Department of Transportation’s ancillary structures for the good, fair and poor categories. Percentage and count for each category are included for the following categories: signs and luminaires, signals, and camera poles and high mast lights with subcategories of foundation and superstructure in each.
For ITS assets, the agency follows an interval-based approach. Information on the age, expected useful life, and recommended cycles of preventive maintenance and replacement for ITS assets is used to develop a maintenance management model that generates needs information. Investment activities for ITS assets include repair and replacement to restore a damaged or deteriorated asset to standard design, functionality, and capability.
Reactive Maintenance Management
When the information on an asset is limited, the risk of failure is low, or the cost to collect data (including condition) is high, then a reactive approach to repair and replacement may be appropriate. Although reacting to asset failure has the benefit of maximizing the life of the asset, from a risk perspective, this approach should consider the time required to repair the system and the impact of that down time. When deciding to take a reactive approach (figure 9), agencies should consider that ITS asset failures can introduce major safety and operational issues (i.e., dynamic message sign fails) or less critical failures (i.e., system communications fails but has minimal impact on actual operations). A failure can be identified in a number of ways, commonly including through sensor detection or public complaints.
Figure 9. Graph. Reactive maintenance management.
(Source: FHWA.)
A line graph showing condition of an asset over time with reactive maintenance. The asset completes the full curve from new condition to failure (end of life) and only at that point does it meet the treatment timing based on asset failure marker at which point it is either replaced or repaired and goes up in a straight line to the initial starting point of the first arc on the x axis and then continues a new arc decline.
Predicting Performance of ITS Assets (Communication Devices)—Austroads
The Technical Supplement to the Austroads Guide to Asset Management provides a list of common approaches to predicting the service life of assets including:
- Manufacturers’ performance data.
- Professional judgment of agency staff.
- Literature reporting service life experienced by others.
- Documented road agency experience: for example, historical databases or other records of asset performance and service life.
- Lifecycle cost analyses to compare the performance and costs of alternative components.
- Predictive models or management information systems to support the management of these assets.
This guide also provides an overview of likely failure modes, methods for predicting service life and the data required for monitoring. The performance prediction for ITS assets (in this example, communication devices) is provided in table 9.
Table 9. Predicting performance of intelligent transportation systems assets (communication devices).
Asset |
Asset Lifecycle (Physical) Performance “Failure” Mode(s) |
Predictability of Physical Service Life of Asset |
Data Required for Monitoring |
Electronic communications infrastructure:
- CCTV camera equipment.
- Electronic signs.
- Electronic speed zones (including school zones).
- Ice detection and warning stations.
- SCATS regional computers.
(partial list included here) |
- System failure due to damage/deterioration.
- Damage from vehicle crash or vandalism.
- Technical obsolescence.
|
- Professional judgment based upon local experience, manufacturers’ data on life of components and monitoring.
|
- Operation.
- Power supply.
- Condition and cleanliness.
|
Reliability-Centered Maintenance
Given the three maintenance management approaches previously discussed, agencies must decide which one is best for them. A reliability-centered maintenance (RCM) approach can be beneficial here. RCM is the application of engineering principles to manage the consequences of failure. The RCM process also invokes engineering reasoning to establish the appropriate maintenance tasks for a given asset. It can be used to select the preferred maintenance management approach for an asset. An example of this is shown in figure 10.
Figure 10. Flowchart. Maintenance Approach Decision Tree.
(Source: FHWA, 2019.)
The RCM process has been used in defense, airline, and mining industries to improve the reliability and cost effectiveness of maintenance activities. RCM is relevant to these industries because of the use of complex electronic and communication equipment that needs to work in an integrated manner.
The following discussion draws from an Austroads report, Reliability-Centered Maintenance Strategy and Framework for Management of Intelligent Transport System Assets (Austroads 2016), which further defines RCM and identifies key success factors, benefits, and acceptance of RCM approaches. The basic steps of RCM involve a set of questions as follows:
- Under what circumstance can an asset fail that may lead to major economic, environmental, operational, and safety costs?
- What are the root causes of the failure?
- Can the failure be viably managed through proactive maintenance? If yes, it is best to minimize the possibility of the failure through proactive maintenance techniques, including on-condition maintenance and preventive maintenance.
- If proactive maintenance is neither technically nor financially feasible, then identify the best alternative maintenance task, which could be a combination of tasks, including the following:
- Unscheduled maintenance.
- Equipment redesign.
- Failure-finding tasks.
- Modifications to operating procedures.
- No scheduled maintenance (i.e., make no effort to anticipate).
As part of Austroads’ RCM study noted above, a number of ITS assets were considered as case studies. A group of practitioners went through the RCM process for these assets. Table 10 illustrates some of the key findings, specifically in this case, for communication systems (a type of ITS asset).
Table 10. Austroads reliability-centered maintenance process.
Item |
Description |
Component |
Communication systems. |
Function |
To relay instructions to the variable message signs (VMS) to display the correct or suitable messages. |
Functional failure |
No or degraded signals received which may cause the VMS to blank out or to display incorrect messages. |
Most prominent failure mode |
- Cellular quality reduced due to high communication traffic—issue in urban areas rather than regional/rural.
- A noise-to-signal ratio increased due to rain/bad weather in another location (communication may recover once weather has passed).
- Problems with connectors.
- Problems with the modem.
|
Failure effect |
Message not displayed to motorists and may cause motorists to be unaware of upcoming hazards such as work zone, closed road, etc. |
Determine criticality: Failure consequence |
Not severe to severe, depending onsite and use. |
Determine criticality: Likelihood |
Likely. |
Determine criticality: On-condition maintenance task |
Replace cables on first sign of deterioration—between processor and modem, cabinet, and VMS. |
List possible task (if applicable)—On-condition maintenance task |
Replace cables on first sign of deterioration—between processor and modem, cabinet, and VMS. |
List possible task (if applicable)—Change operating procedure |
- Fall-back mode for situations when communication is down.
- Redundancy in communication service.
|
List possible task (if applicable)—Fault finding (testing) |
- Remotely checking for communication faults.
- Increase access for operations and maintenance teams to back-end communications and data logs to increase efficiency and fault-finding efficiency.
|
List possible task (if applicable)—Equipment redesign |
- Enhance self-correcting features to reboot/restart communication systems to re-establish communications with the VMS.
- Improve ruggedness of connectors (resistance to corrosion and vibration).
- Install lightning arrestors.
- Redesign cabinet and hardware so that third party components (such as modems) are not inside the cabinet (i.e., inspections can be done without requiring maintenance staff to unlock the cabinet).
- Implement Web-based interface for VMS services to allow Roads and Maritime to upgrade firmware remotely.
- Consider alternative wireless connections, such as Bluetooth and Wi-Fi.
|
List possible task (if applicable)—Call-out maintenance |
Conduct call-out repairs as currently practiced. |
Remarks |
Communication faults due to issues with the signal carrier happen regularly and randomly. Communication systems are set up to automatically reset themselves and re-establish connection. The reliability of signal carriers is improving, and the significance of this issue may reduce in the future. No further actions would be required apart from improving the automatic reset capability of devises. For critical sites, install redundant communication access. Issues with connectors need to be addressed through appropriate redesign and installation. Improvements in automatic and remote fault testing are also valuable to quickly identify sites that require repairs. |
Obsolescence
ITS assets can become obsolete even if the asset is in good physical condition and functioning as designed. With rapidly changing technology and expectations of the traveling public, the technological demands of the transportation system may exceed the asset’s capacity to provide the necessary service.
For advanced technology that is commonly found in ITS assets, obsolescence is a challenge. For example, an asset can become obsolete if:
- It needs to be replaced due to other projects (e.g., road widening).
- The software or the product is no longer supported by suppliers, and software upgrades or replacement parts are unavailable.
- The cost to repair becomes greater than the cost for replacement (and often improved) products.
- The software is no longer compatible with new systems.
The challenge with obsolescence is that it is hard or impossible to predict. It can shorten the expected life of an asset and mean that it needs replacement before it reaches the point of failure. Sometimes, upgrades in the asset or even software can have a net benefit to the mobility and reliability of the transportation system in addition to cost savings, even if the current setup is meeting the demands of the system. Agencies are starting to identify strategies and steps to better plan for obsolescence, which typically follows a risk-based approach:
- Asset Lifecycle—Determine how long the asset should be sustained and operated, considering any major mid-life upgrades or replacements.
- Identify Components Most Likely to Become Obsolescent—Breakdown the asset into its lowest maintainable units, or components. Most obsolescence issues are experienced at the component level.
- Develop Criteria to Assess Obsolescence Risk—Identify various factors the agency can use to determine the probability of an obsolescence issue and/or the operational impact, if the component were to become obsolete. This might include number of manufacturers, access to software upgrades, and ease of replacement.
- Assess the Risk of Becoming Obsolete—For each component, based on the criteria developed, assign a score (such as low, medium, or high) for both probability and impact and calculate an overall obsolescence risk score.
- Mitigation Strategies—For those components identified as high obsolescence risk, determine appropriate mitigation strategies, such as design considerations, planned system upgrades, and partnership agreements with suppliers.
Lifecycle Planning
As defined in 23 CFR § 515.5:
Lifecycle planning means a process to estimate the cost of managing an asset class, or asset subgroup over its whole life with consideration for minimizing cost while preserving or improving the condition.
The process of lifecycle planning considers a range of different maintenance management approaches to deliver the most cost effective solution throughout the life of the asset. Lifecycle planning identifies the costs and outcomes associated with a range of maintenance management approaches. This information then is combined with:
- Existing condition information.
- A deterioration rate for assets that assesses how quickly the condition of an asset falls from one condition level to another. In an age-based model, this will purely be the time to move from one condition level to the next.
- An analysis period that is usually at least as long as the time from asset creation through to asset rehabilitation or replacement.
The FHWA guidance Using a Lifecycle Planning Process to Support Asset Management (FHWA 2017) addresses developing an initial lifecycle planning process that satisfies the requirements of 23 CFR part 515.
Lifecycle Planning Model—Caltrans
The Caltrans TAMP has four primary asset classes: pavement, bridge, drainage, and Transportation Management Systems (TMS). California TMS assets include (but are not limited to): traffic signals, closed circuit televisions, changeable message signs, traffic monitoring detection stations, and freeway ramp meters. As shown in figure 11, California’s lifecycle planning model for its assets is based on the costs and service life of different types of treatments (currently, for TMS assets, the “Fair” state is not yet applicable). This lifecycle planning model is founded on the principle of deterioration. Deterioration is the physical degradation of an asset because of a combination of factors, including age, construction materials, environment, accidental damage, and traffic load. A set of deterioration rates are determined for each asset type to account for expected future conditions.
Caltrans currently uses a TMS Inventory Database populated by district personnel to track all statewide TMS assets. This database provides information on system type, location, and installation date. Caltrans is developing strategies to better monitor the condition of the TMS network, such as strengthening collaboration with maintenance staff, which will enable a more responsive and efficient replacement process.
Figure 11. Diagram. Caltrans physical asset model for lifecycle assessment.
(Source: Caltrans, 2018.)
A diagram showing the lifecycle of an asset. From right to left there is good, fair and poor categories. From left to right there are arrows showing the deterioration trend over time as they downgrade from good to fair to poor. Underneath the three categories there are arrows moving from right to left showing the improvement of fair and poor assets to good as they are repaired or replaced over time and become good assets in good condition again.
Lifecycle Planning for ITS Assets—Nevada DOT
Nevada DOT follows an interval-based approach when it comes to its ITS lifecycle planning. Each ITS asset is categorized based on its remaining service life, and then the agency conducts maintenance and management activities based on the following categories:
- Inspection—Routine device maintenance, performed annually or biannually.
- Minor Repairs—Work performed onsite, such as adjusting cables, replacing batteries, and upgrading firmware.
- Major Repairs—Work that requires the device to be sent to the maintenance shop or factory for repairs and involves replacement of one or more key parts.
- Replacement—Involves complete removal and replacement of the device.
Table 11 shows the impacts of the type of maintenance activity on the existing condition states. For instance, an ITS asset in good condition may only be inspected periodically. If the inspection indicates that the asset is a low risk, minor repairs could be applied to bring that asset back up to good condition. Similarly, if an ITS asset is a medium risk, major repairs could improve the status to low risk.
Further, Nevada DOT conducted a study to determine the effectiveness of its current ITS maintenance strategy versus a “worst-first” approach, where the devices would receive no minor repairs or maintenance and would simply be replaced after they fail. Figure 12 shows the annual maintenance cost per device (in 2015 dollars, excluding initial installation costs).
Table 11. Nevada Department of Transportation maintenance activity impact matrix.
Current Condition |
Condition After Inspection |
Condition After Minor Repair |
Condition After Major Repair |
Condition After Replacement |
Good |
Good |
— |
— |
— |
Low Risk |
Low Risk |
Good |
— |
— |
Medium Risk |
Medium Risk |
Medium Risk |
Low Risk |
— |
High Risk |
High Risk |
High Risk |
Medium Risk |
Good |
Figure 12. Graph. Nevada Department of Transportation intelligent transportation system asset lifecycle analysis comparison.
(Source: Nevada Department of Transportation, 2019.)
A bar chart showing a comparison analysis of intelligent transportation system (ITS) asset lifecyles. Annual cost per device is plotted on the x axis in dollars for worst-first strategy versus Nevada Department of Transportation's current strategy for the following categories: closed caption television (CCTV), dynamic message signs (DMS) flow detectors, highway advisory radio (HAR), ramp meters, and road weather information system (RWIS). The worst first strategy is almost three times higher for DMS, and almost double for CCTV and flow detectors, and just a bit higher for HAR, ramp meters and RWIS.
Building Information Modeling as a Tool to Inform Lifecycle Planning
One factor that can affect maintenance and operations of ITS assets during the lifecycle is how it is inventoried, particularly in capturing key attributes, such as location data. Most agencies manage the inventory of ITS-enabled intersections or sites, but not the individual components at the site (e.g., controllers, signals, poles, and cabinet equipment). Critical data about ITS assets and components, such as manufacturer details; type of device; warranty period of installed device; and maintenance recommendations, schedule, and activities, are typically not captured after installation, but this information is important for operations, periodic maintenance, and proactive work-planning.
Issues such as those stated above can be addressed by incorporating Building Information Modeling (BIM) processes, policies, tools and standards. BIM integrates many technologies and practices that bring digital tools and a data-centric approach for improving lifecycle delivery and management of highway assets. However, the approach for deploying BIM has been typically siloed, either within an organization’s subunits or at the project level. Many State DOT's recognize the benefits associated with the bigger picture of BIM as a data-centric approach, both for project delivery and asset management practices. BIM centers on the idea that data itself is an asset, and that there are efficiencies to be gained when business silos are broken down so that data is accessible throughout a project and asset lifecycle.
Examples of BIM use include:
- Contractors installing the ITS assets/infrastructure can be required to submit information about the installed (as-built or as-rehabilitated) assets in a prescribed format (typically a spatial data file with relevant attributes). These are referred to as “Employer Information Requirements” (EIR) in the BIM world, and can be set up as a legal/contractual requirement. The data requirements can vary depending on the type of work (new installation, modification, rehabilitation, component replacement, in-house maintenance). In addition to contractors, the requirements can also be established for in-house maintenance crew.
- Tools such as mobile apps for ITS data collection can be deployed for meeting the EIR requirements at each stage of the lifecycle, especially when contractors or maintenance crews are changing any aspect of the installed infrastructure.
- Requirements used to build the computer-aided design (CAD)/BIM data model created with CAD or BIM standards during the design phase. To meet the EIRs, the as-designed models can be updated after construction to create the asset as-builts. Across the various design stages, construction, and operation/maintenance stages, interoperability or exchange of these data models would ensure that information is constantly added to create and update the data model. In fact, information about the timing and cost of the installations for each asset should be captured in the model. Software systems used during design, construction and operation/maintenance phases should be able to accept models in open standards.
- Policies and processes should be in place to ensure that employees understand what data needs to be captured when and how.
Key Actions
Agencies can adopt or improve upon several key actions when working toward maximizing performance through lifecycle planning for ITS assets.
Understand the Outcome from Alternative Maintenance Management Approaches to Lifecycle Planning
Understand the outcomes of different maintenance management approaches to be able to demonstrate cost effective practices and inform investment strategy decisionmaking.
Key Steps:
- Understand the available maintenance management approaches (condition-based, interval-based, reactive) for each asset/component.
- Assess the lifecycle cost of different maintenance management approaches.
- Consider the risk that obsolescence introduces to different approaches.
- Utilize analysis to inform investment decisions (see subsequent section).
- Implement and continually revisit the selected management approaches. Consider how detailed asset information (e.g., age, condition, cost) may help influence lifecycle planning decisions and consider changes to asset inventory collection if appropriate.