STEP 5 – SYSTEM DEPLOYMENT
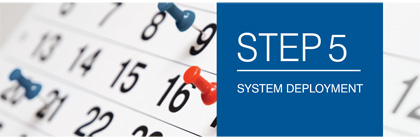
The planning, design, and procurement efforts culminate in the actual deployment of the selected work zone ITS. Although considerable effort may have already gone into earlier steps in getting ready for deployment, this is the point at which things can really get busy. Unlike permanent ITS deployments which are typically the objective and focal point of efforts, a work zone ITS deployment must be matched to the overarching goal of completing whatever construction project or projects are necessitating the work zone in the first place. A work zone deployment becomes another cog in the overall project to be coordinated, managed, and otherwise adjusted so as to achieve the main desired goal: to complete the tasks required correctly, on time, and within budget while at the same time minimizing the impacts of those tasks upon the public, especially the traveling public.
As those who have been involved in performing and completing a work zone project can attest, project coordination involves chasing a constantly changing target in many cases. Field changes in project scope, phasing, scheduling, etc. can all affect how a work zone ITS component fits and will work as a mitigation strategy. Even if such changes in a project do not occur, it is not known for certain how effective a particular ITS application will be until it is deployed. Consequently, field adjustments to the system are often necessary. Additional equipment may be needed because impacts exceed what was anticipated, or system operation may need to be altered to improve driver understanding and response to the system. These changes may be needed immediately upon deployment, or develop when the project changes to a new phase with a different maintenance-of-traffic (MOT) approach. As such, system deployment is not so much as step as it is a process.
System deployment includes initial implementation, as well as scheduling decisions, systems acceptance testing, and handling major deployment issues, as depicted in Figure 20. Deploying the system should be done in coordination with the deployment of other TMP strategies.
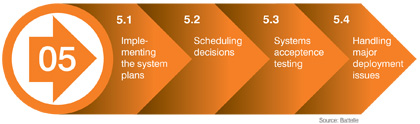
5.1 Implementing the system plans
The role of an agency during system deployment depends on the size and complexity of the system, whether it is a COTS system or a unique system designed to address a highly specialized need, and whether it is to operate independently or be integrated into other ITS operational components in the region. For small, COTS systems that are intended to operate independently, agency involvement during deployment may consist of the project engineer and inspectors keeping track of the system and monitoring and validating the information being collected and disseminated. For larger and/or more novel or complex deployments and deployments that involve integration with existing ITS components, the level of agency involvement may span across several offices and divisions, and require significant staff time to test, troubleshoot, validate, monitor, and maintain the system.
Personnel with expertise in ITS deployment must be available through all steps of the deployment. For COTS systems, that expertise often resides with the vendor; for customized system designs, such expertise may need to reside with the agency or the consultant hired to design and oversee the deployment of the system. For customized system designs or deployments that are connected to existing permanent ITS infrastructure, it is also vital that key staff understand the overall vision developed in Step 2 and the requirements defined in Step 3. Subcontractors may look at each requirement individually, but not take into account the overall system vision. Such a “stove pipe” analysis can result in an installation that, while consistent with the literal system requirements, does not support the overall vision and other TMP strategies as intended.
5.2 Scheduling decisions
Scheduling can play a major role in the deployment of ITS applications for work. Testing and ultimate system calibration can take longer than anticipated, for example. It is critical that a work zone ITS deployment be available and functioning at the beginning of a project or major phase change for which it is intended, as this is the time when drivers first encounter unexpected conditions and need real-time information.
Scheduling decisions could include:
- Plan for sufficient lead time to deploy: Some agencies that are incorporating work zone ITS deployments into their construction contracts require that the system be operating before actual construction work starts. Contractors need to allow sufficient time for this requirement in their overall project scheduling. Agencies or their consultants who are deploying work zone ITS themselves to support a particular project need to plan sufficient lead time as well.
- Plan for sufficient calibration time and effort: Systems that provide real-time travel time and delay information to motorists typically require some level of calibration to fine tune the values presented. Normally, this will need to occur after work and its associated congestion have begun. Efforts should be taken to ensure the availability of staff to assist during the calibration process very early in the project. Continued display of inaccurate travel times or delays will significantly erode credibility of the system with drivers, and make it more difficult to get drivers to react to the real-time information.
- Consider the potential for the unexpected to occur: It can be difficult to predict in advance the traffic impacts that a work zone might generate, and thus the amount of coverage needed for a work zone ITS deployment. It can be beneficial for agencies to have contingency plans, or at least have options available to them, with regards to modifying the system slightly. For example, an agency can designate that the contractor obtain an initial work zone COTS system meeting a set of specifications and equipment requirements as part of the original bid process. However, if additional equipment or functionalities are later found to be required, the potential implications for using a change order process to obtain that additional equipment or functionality should be thought through.
Agencies should ensure that as much time as possible be built into the implementation process and construction schedule, especially with regard to system calibration and sensor programming. Systems can be developed and deployed in short timeframes when needed. Additionally, flexibility is important for the ITS deployment schedule due to uncertainties in the construction project schedule. The initiation or conclusion of a construction project, or individual phases of a project, often change due to a variety of factors. While delays may be more common, sometimes projects or project phases can begin or end earlier than planned with only short notice from the construction contractor or agency staff. If ITS changes are necessary between phases, paying closer attention to the schedule is warranted to minimize ITS downtime. On the other hand, the steps outlined in this guide do require time to complete, and so it is important to allow for sufficient time.
![]() |
Problems will arise—such as the operation of sensors, communications (wireless or wired), calibration, or software—and will take time to address. These “bugs” require time to locate and address. Failure to allow for sufficient start-up time can lead to less than optimal performance of the system during the initial days of the project. Unfortunately, this is often the time at which the system is most needed, as drivers are encountering unexpected conditions due to the capacity and operational constraints imposed by the MOT plan, are surprised, and need and would benefit significantly from having improved information and guidance in how to best accommodate the work zone. |
![]() |
Although it is desirable to begin the process for considering, planning, designing, and deploying a work zone ITS early in the overall project development process, circumstances sometimes dictate that an accelerated timeline be followed. It is important to recognize when such circumstances arise and to dedicate enough resources to be successful in meeting that timeline. For example, a work zone ITS deployment used on the Big I (I-40) project in Albuquerque, New Mexico, was able to go from concept to full operation in only 15 weeks. However, to accomplish this, the agency had to employ several experienced ITS contractors for the ITS design, system selection, and system installation. |
5.3 System acceptance testing
Before the work zone ITS is activated, system acceptance testing must be conducted. These tests should be comprehensive to ensure that all system requirements and user needs are met. System acceptance testing will follow the testing strategy proposed in substep 3.3 and will validate the functionality and accuracy of the work zone ITS to make sure the system is working as planned.
Following the test plans from substep 3.3, data sheets should be used to record test data and compare recorded results with expected results. Test reports should be compiled that document how well the system performed and any modifications that need to be made prior to system activation.
As applicable, driver capabilities should be re-examined at this time to verify that the system will be satisfactory from a human factors perspective. Messages displayed on CMS should follow current guidance to ensure that the information is clear, concise, and credible. Characteristics of the devices and their deployment locations should also be checked. For example, the size of the text on a message display must be sufficiently large and visible (a minimum of 18 inch characters for freeway conditions) so that drivers do not have to slow down to give themselves more time to read. Message boards should be checked to be sure they are positioned away from obstructions that might limit viewing times, such as piers, abutments, parked construction equipment, etc.
5.4 Handling major deployment issues
Issues identified in system acceptance testing that are likely to affect deployment include problems with communications, power, sensors, and other system components deployed in the field. Communications can especially be a challenge in rural areas. While it is impossible to anticipate every possible contingency that could arise during deployment, availability of staff experienced in the deployment of ITS is one of the best means of mitigating issues that arise during deployment.
The key is to prevent issues from arising in the first place by selecting an experienced/qualified contractor and providing sufficient time within the schedule to handle issues that are not anticipated. Maintaining flexibility is crucial, as unexpected things like parked construction vehicles, construction equipment storage, or law enforcement positioning in front of sensors can cause issues that will need to be addressed. Developing and sustaining good working relationships among project team members are helpful for when issues arise. Frequent communication within the team can also assist in this process by helping to establish a positive working relationship among contractors, ITS subcontractors (if used), and government agencies.
Other issues like construction design or plan changes can also affect the ITS deployment. For example, an initial decision to keep a particular entrance ramp open during a major freeway reconstruction project may be changed based on poor safety performance of similar entrance ramps experienced at an ongoing project immediately upstream. If the initial decision was to deploy a work zone ITS with temporary ramp metering at that entrance ramp, the ramp metering component might need to be eliminated.
Key Takeaways |
|
![]() |
Utah used performance-based specifications for work zone traffic control during a design-build project on SR 154 (Bangerter Highway) in Salt Lake City, developing and implementing a travel time monitoring system that used a Bluetooth address matching system. Utah DOT and the contractor spent a considerable amount of time once the antennas were deployed to fine-tune the overall operation of the system. A number of settings on the devices themselves had to be calibrated depending on how traffic was behaving near the antenna itself. Some of the calibration involved settings on the antenna itself, others in terms of how the data coming in from the detectors are handled during processing. It took the Utah DOT/contractor team a significant amount of time to understand the nuances of the system and to get the system to operate as desired. Another aspect of system operation that took some time for Utah DOT and the contractor to reach a consensus on was the minimum number of Bluetooth matches between antenna locations needed in a given time period to develop a good travel time estimate. Once calibrated, the system worked as intended, and yielded significant benefits to both Utah DOT and the contractor. |