National Coalition on Truck Parking: Parking Capacity Working Group Meeting 2 - February 14, 2018
Printable Version [PDF 485 KB]
You may need the AdobeĀ® ReaderĀ® to view the PDFs on this page.
Contact Information: Freight Feedback at FreightFeedback@dot.gov
U.S. Department of Transportation
Federal Highway Administration
Office of Operations
1200 New Jersey Avenue, SE
Washington, DC 20590
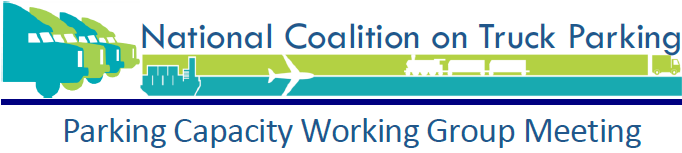
February 14, 2018
A recording of this meeting is available upon request.
Champion:
- Brian Hunter, Florida Department of Transportation (DOT)
Facilitators:
- Tiffany Julien, FHWA
- Jeff Purdy, FHWA
- Jordan Wainer, Volpe
Welcome and Introduction
Brian welcomed the group and asked everyone on the phone to introduce themselves. He also noted that the meeting notes from the first Working Group meeting are in draft form and should not be distributed, since they are currently under review by the Office of Public Affairs.
Champion Meeting Debrief
Brian met with Tiffany Julien (FHWA), Jeff Purdy (FHWA), Jordan Wainer (Volpe), and Kara Chisholm (Volpe) following the first meeting of the Working Group to discuss in more detail the priority area products identified in the first Working Group meeting. Brian reiterated that the ultimate goal of the Working Group would be to build more truck parking, but since there is insufficient funding available to make that possible, the group has to develop other methods of increasing the supply of truck parking. Brian reminded the Working Group that during the first Working Group meeting, the Group identified four priority areas that it would like to focus on (listed below). However, he mentioned that the Working Group will set aside the "Explore flexible funding opportunities" priority area because the Funding, Finance, and Regulations Working Group will be researching the same topic.
Priority Areas Established in First Meeting
- Involving shippers/receivers.
- Exploring flexible funding opportunities. The Working Group will set this aside and allow the Funding, Finance, and Regulations Working Group to research the topic.
- Creative use of Right of Way (ROW).
- Low-cost truck parking.
Jordan introduced the next stage of the Working Group meeting, which was to discuss the products that the Working Group will create in order to address the Working Group's priority areas. Brian named each Priority Area Product and solicited examples from the Working Group members. The priority area products and the relevant case studies, resources, or best practices for each one, as well as some related discussion by Working Group members, are listed below.
Potential Priority Area Products
- Create a hybrid list of case studies and resources on involving shippers/receivers.
- Meijer grocery stores provides a truck parking bullpen adjacent to the entrance to the distribution centers. They allow drivers to park outside the fenced-in delivery area if they recently made a delivery or are going to make a delivery. Being outside the actual delivery facility could help limit liability for the company. There is usually a Port-o-John in the parking area for use by drivers, and there is also a guard shack.
- Walgreens distribution centers in Marina Valley, California have worked with Police in the area to locate streets with low traffic and have designated them as parking areas for trucks, for staging use only. Signs have been erected on these streets to make clear that they can be used by truck drivers for staging purposes. Drivers are not allowed to park on the Walgreens lot. There are many distribution centers in the area, which is all industrial.
- Unilever's Safe Haven program allows parking at their distribution centers. The program has been in operation for two years and there haven't been any incidents so far. Unilever allows parking on-site at the shipper or receiver, or in some cases, Unilever provides parking just outside, adjacent to its shipping/receiving area. Unilever has been working with an application-based load matching service to make sure the application shows that the facility has parking affiliated with it. Drivers don't necessarily have to make reservations to use these facilities; it varies facility to facility. The motivation for Unilever instituting the Safe Haven Program and working with the application-based load matching service is for Unilever to become the "shipper of choice" for drivers. Advertising for the program is mostly through the application-based load matching service.
- Weed, CA is located off of interstate 5 and has developed a municipal parking lot that is reserved for truck parking. The parking lot consists of about 30 spaces and is near a Pilot truck parking facility. The purpose of choosing that location was to provide drivers with access to amenities at the Pilot and other adjacent restaurants. The town hasn't had any enforcement issues since providing this free parking.
- Elmira, NY, located off of interstate 86, created truck parking off of an existing carpool parking lot. The municipality provides about 25 truck parking spaces. The city charges for parking there. The cost is $5 for 24 hours, $30 for a week, and $50 for a month. This is particularly helpful to truck drivers who live in the vicinity. Citizens stopped complaining about trucks once parking was made available.
- A Working Group member has spoken with a local Walmart distribution center regarding its business model as it relates to shipping costs. Walmart's shipping costs are included in the overall costs of the order placed with a supplier. The structure of this arrangement doesn't provide much incentive to improve parking facilities located on their properties. The Working Group member believes that providing shipping Safe Havens would decrease Walmart's overall costs as well as make the shipping process more reliable and more desirable. He would like to discuss this further with Walmart.
- A Working Group member shared that Walmart recently updated its regulations to require that drivers arrive within one hour of their scheduled check-in time, or face a fine. In order to comply with Walmart's rules as well as the Electronic Logging Device mandate, drivers have to be very strategic about their routes and time on the road. The Working Group Member believes that Walmart's regulations that impact truck drivers require related concessions to be made by the company in order to assist truck drivers in complying with the company's regulations. The Working Group member recommends that local and State governments get involved to pressure Walmart to provide parking or staging areas for drivers. For example, the Fairhaven distribution center is located close to an abandoned lot that could be used as a staging area. Making use of places like this would be helpful.
- Another Working Group member agreed with the observation about Walmart, and noted that many shippers and receivers believe that providing truck parking is the responsibility of government. The Working Group member believes that, in actuality, providing truck parking is a cost of shippers and receivers doing business, and should be treated that way.
- CenterPoint, a distribution hub located outside of Chicago, offers paid parking, by reservation.
- Walmart Distribution Center in Apple Valley, CA has its own access road with plenty of parking area along the road, but the distribution center does not allow truck parking. It is not a residential area, so it could serve as a staging area. The Working Group member believes that drivers would be willing to pay to park at those areas.
- Brian asked Working Group members whether they had the contact information of any developers of large industrial areas, so that the Working Group could ask them how they make decisions about how to size their truck parking areas. None of the Working Group members provided a contact.
- Brian asked the Working Group for examples of large industrial areas, such as CenterPoint, that have become popular recently, and whether those facilities provide truck parking.
- A Working Group member shared that in order to promote truck parking, local governments should ensure that new industrial developments include adequate truck parking. It would be useful to provide local governments with a checklist of items to look for from developers.
- Develop a one-pager to highlight the more creative uses of Right-of-Way (ROW), State by State.
- Missouri closed outdated rest areas and turned them into truck parking areas, adding about 1000 spaces. The obsolete rest areas facilities were removed and replaced with lower-cost vault bathrooms.
- South Dakota and other western States have created dedicated truck parking in pull-off areas in the right-of-way (ROW) along some rural sections interstate.
- Miami, Florida has created an area from an old park-and-ride facility in Miami where Turnpike-double trailer trucks breakdown their tandem and go to single for last mile deliveries. Planners are looking at densifying that facility, moving a lot of the park-and-ride to the other side, and building a truck travel center third-party logistics (3PL) facility.
- Maryland allows trucks to park in park-and-ride lots during inclement weather. Maryland also permits truck parking at weigh stations, such as the one in Perryville. Drivers are reluctant to use the weigh stations, though, because they fear being called in for inspection.
- Kentucky allows parking at four weigh stations and also has signage with a specific icon to denote available truck parking at the weigh stations. The signage makes it very clear that truck parking is allowed, so this might be a method for encouraging reluctant truck drivers to take advantage of available parking at weigh stations. It would also be helpful to use this icon consistently around the country.
- One Working Group member noted that almost all States allow parking at weigh stations.
- Tampa, Florida is installing restrooms and showers and truck driver convenience areas at weigh stations on Interstate 4, just east of Tampa.
- Florida offers paid parking at farmer's markets owned by the Department of Agriculture.
- Houston, Texas and West Palm Beach, Florida have private business with truck lots that rent spots out by the day or the month. Many have dirt lots, and are looking to advertise to drivers.
- Big Springs, Nebraska has truck parking on a half clover leaf interchange where Interstate 80 and US 138 merge. The center of one of the interchange loops is gravel, and each night 100-200 trucks park there. The State owns the land and it appears to be a very low-cost option.
- Minnesota Department of Transportation has an agreement with the local Chamber of Commerce to create a Tourism Center on US 371 that includes truck parking. Truckers are able to get in and out of that area within the ROW, and the tourism chamber operates that facility. The Working Group member said that it is a nicer facility than a standard rest area. Link to the facility's website: http://www.explorebrainerdlakes.com/brainerd-lakes-chamber/.
- Investigate the burdens and potential solutions for maintaining low-cost truck parking facilities.
- Brian stated that often resistance to providing truck parking often includes the idea that the parking areas will need to be maintained by providing trash removal and toilet facilities. He asked the Working Group members to provide examples of other common concerns about maintaining and operating truck parking facilities, and possible solutions to those concerns.
- A Working Group member stated that some costs of maintaining a low-cost truck parking facility are trash removal, snow plowing, and ice removal.
- Wyoming has pull offs along the interstate that allow 5 to 15 trucks to park. The State DOT needs to regularly clean up litter at these sites.
- Texas uses dumpsters for trash collection. One participant noted that drivers might be willing to pay to use the dumpsters.
- Better signage could be a low-cost way to inform truckers of available truck parking facilities.
- States could have an organization such as a State trucking association adopt a truck parking facility and take care of trash cleanup in order to minimize costs.
- One working group member suggested that facility operators institute additional enforcement of proper trash disposal amongst drivers.
- It's less expensive to operate a truck parking facility than a full rest area facility. The cost to convert a rest area to a truck parking facility is low. Operating a truck-only parking facility requires emptying the vault toilet once a month and emptying the trash once a week. The cost of operating a truck-only parking facility is about $30,000 per year, and operating a rest area is about $300,000 per year.
- One Working Group member noted that the cost of plumbing and toileting can be a deterrent, so some States are choosing to use vault toilets at lower-use facilities.
- Truck parking areas could use soil-cement instead of gravel as a low-cost paving material. It doesn't get as rutted at gravel, but it also is not well-suited to climates where there is frequent freezing and thawing.
-
Flexible funding opportunities.
- To be investigated by the Funding, Finance, and Regulations working group.
Brian then transitioned the discussion to the next steps for the Working Group, which consisted of providing a summary of the examples and case studies provided for each priority area product, as well as listing action items for Working Group members for the next Working Group meeting.
Next Steps
- Working Group members will gather written resources or points of contact pertaining to the hybrid list of case studies and resources on involving shippers/receivers product.
- One Working Group member volunteered to set up a template for gathering examples about creative uses of the ROW and how to populate it.
- One Working Group member volunteered to gather information for a one-pager about the truck pull off parking in Wyoming.
- One Working Group member will find specifications for the soil-cement paving material.
- Working Group members will send all the above information to Brian Hunter and Jordan Wainer by Friday March 9th.
- Jordan gave an overview of the plan for the Working Group over the next several months, including that there will be two more meetings of the Working Group, in April and June. The overall goal of this effort will be to have all four Working Groups present their final products to the larger National Coalition on Truck Parking members at the annual meeting in the fall.
- Volpe will aim to have compiled the resources and examples it receives from Working Group members into draft products by the next Working Group meeting.
Brian asked the Working Group members whether they had any questions to raise prior to calling the meeting to a close. Hearing none, Brian ended the meeting.